Vacuum dewatering flooring
The vacuum dewatering process basically improves strength, durability, and other properties of concrete by reducing the water-cement ratio immediately after the mix is placed, usually in floors and other flatwork. A Bridgeport, Connecticut vacuum dewatering demonstration, although it involved no new technical developments, was of interest because the work was supervised by one of the major manufacturers of vacuum dewatering equipment.
Concrete was placed in the slab forms, consolidated with immersion vibrators, then leveled and vibrated again with a double-beam vibrating screed. The vibrating screed was pulled over the concrete surface by two men. After screeding, the concrete was immediately covered with a filter pad and a suction mat connected to a vacuum pump. Within seconds the vacuum created under the mat began to compress the concrete and cause water to be drawn through hoses to the suction pump.
Vacuum was applied for about 3 to 5 minutes per inch of slab thickness. Typically, this lowers the water content of the concrete by 20 to 25 percent, while the filter pad minimizes loss of cement fines with the water which is being collected. Less than half of one percent of the cement is ordinarily removed during vacuum dewatering.
After a given area of floor was dewatered, the pad and mat were moved on to another freshly placed section of the slab. The dewatered surfaces were firm enough to be walked on, and were immediately floated with a power trowel fitted with a planning disc to remove any high spots or irregularities introduced during the vacuum processing.
Where skid-resistant surfaces are desired, this completes the floor-finishing operation, and the slab is ready for curing about one-half to one hour after vacuum treatment. Where a smoother surface is specified, power troweling is done, usually 30 to 90 minutes after the planning operation.
Advantages of Trimix flooring or Vacuum dewatered flooring over the conventional flooring:
- Increased Compressive strength of floor
- Increased Tensile strength
- Reduced Cement consumption (No cement is required for finishing the surface)
- Increased Abrasion resistance
- Reduced water / cement ration
- Increased Impact strength
- Reduced number of joints
- Less wear and tear of floor surface
Typical Application Areas of VDF Flooring
- Warehouses, Godowns
- Roads, Sports Courts
- Cellars, Parking Areas
- Production Areas,
- Pharmaceutical Companies
- As the base floor for Epoxy & PU Floorings
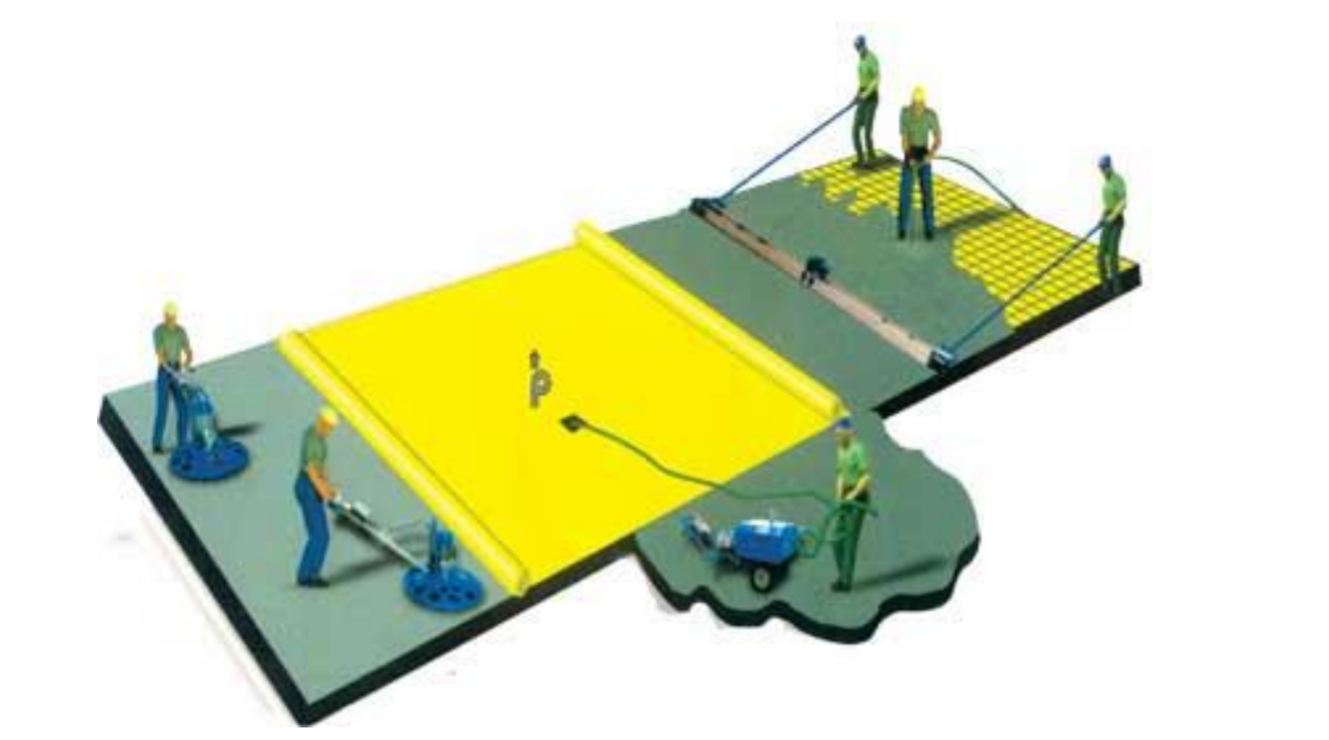
Schematic showing Vacuum Dewatering Flooring Method
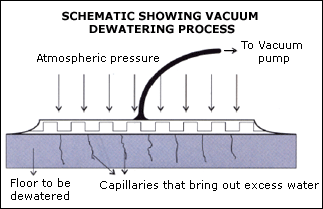